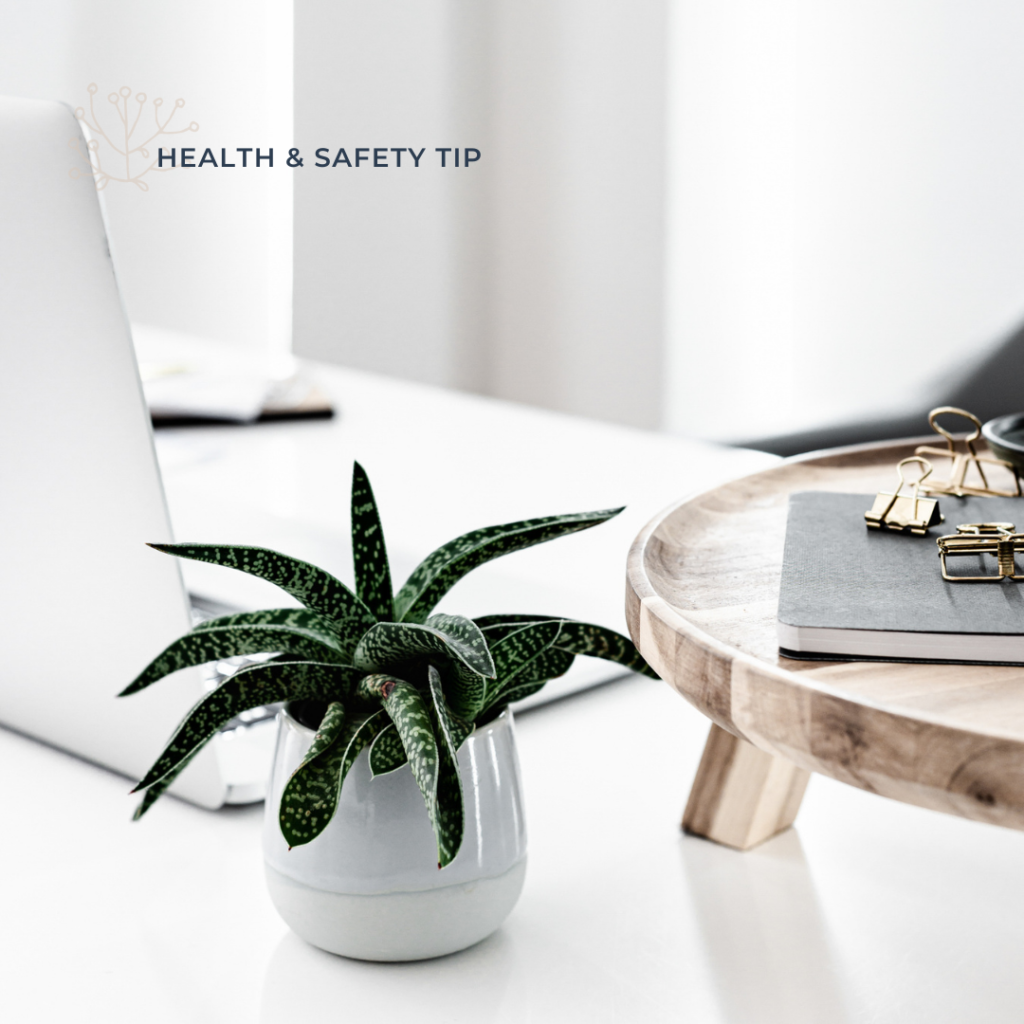
So for some of you, health and safety management is not your forte. I’m here to help!
Let’s dive into 5 tips to make health and safety management simplified.
#1 Policies are the boss.
In terms of who, what, when, where, and why; refer to the policy. Too often, when talking with owners or management, I ask “what does your policy say you have to do in regards to X” and I am answered with a blank stare or a “I don’t know.”
Is this you? I hope not, but if you are – I can help.
When creating a policy don’t just copy/paste from someone else’s or *gasp* use a template you found on the internet because the actions and accountabilities might not match your company.
If your company is seasonal; don’t put that you’ll do weekly inspections because your equipment is parked for months.
If your company does not have superintendents, don’t put that position into your policies.
Bonus tip – team leads are considered supervisors so you’d better train them as such – aka you can call a potato a poh-tah-to or po-tay-toh but at the end of the day you and they still have responsibilites under legislation.
Take the time to think about the WHY when creating or updating a policy; and HOW it will be a value to your business.
As an auditor, the general question is “are they following the frequency stated in their policy?” … so make sure you’re selecting a frequency that makes sense to the job risk ranking and not “as needed” or “on a regular basis”.
#2 Forecast your health & safety costs.
I have lost count of the times where clients do not understand the cost of their health and safety program; if you don’t know the cost then how can you manage it? Stop thinking about health and safety as an “outside of operations” department and create a budget for the elements based on your health and safety manual, and supporting programs.
So you work at heights, an average cost of Fall Protection is $150 / employee; it expires every 3 years; a harness costs $125, lanyard $65, etc
So you have vehicles, an oil change is $90, you expect to drive 40000KM a year based on project travels; you budget for X services every 12,500KM (or manfu recommendation).
So you … get the point, right? If not, I’d love to chat about forecasting health and safety costs so that you can assess your rates accordingly.
#3 – Formal Hazard Assessments.
A properly completed Formal Hazard Assessment for a job position or tasks can provide so much clarity when it comes to the training needed, tools & equipment required, and develop prioritization of the hazards based on the level of risk with the supportive implementation of controls for the identified hazards.
This document foundational to your program and should not be taken for granted.
The mechanisms for reviewing your Formal Hazard Assessments should be located with your policies (they are the boss) and at min cover:
1. When new operations, work processes, equipment, materials or products are introduced.
2. When operations work-related processes or equipment are modified.
3. When site-specific hazard assessments, inspections, or investigations identify a previously unrecognized hazard.
4. As per a set frequency (re: annually / quarterly for high risk work etc).
This list comes from the ACSA COR Audit Tool – refer to your chosen audit tool for specific criteria required within your FHAs.
Creating an inventory of FHA that are current within the job positions / tasks within the organization, reviewing the document with key stakeholders from all levels within the organization, and having a basic understanding of cost to implement the controls within the FHA will help the company be successful, but most importantly will be a tool in creating a healthy and safe workplace.
#4 – Schedule Your Responsibilities.
At the end of the day, you realize that the worksite inspection did not get done or you weren’t able to get the competency assessment completed; and you know that tomorrow (and the next day, and next day etc) is jammed packed with other tasks.
What I’ll say to you is simple – that what you classify as a priority – you get done.
I’ll say that again – what you prioritize, you get done.
So the big question for you is – are your health and safety responsibilities a priority to you?
Now, really think about it to answer honestly. How often do you find the health and safety tasks in your calendar being pushed aside for “operations” or something “more important”? This sends a BIG message to your team about what you think is important to the business.
Whatever task and frequency you set (refer to the policy), make it a high priority on your schedule. Only allow critical tasks supersede the health and safety responsibilities; think about what those might be ahead of time so that you don’t have to think about what is important.
#5 – Continuous Improvement.
Your program should not be static; it should be reviewed, measured against a standard, and updated as required.
As you grow your business, it’s important to update policies, programs, and procedures so that they support the business direction and ultimately drive you towards your business goals.
What worked for your business 5 years ago, or even three months ago, might be working against your business today.
Set time to conduct internal audits; or hire an external consultant (hint hint) to help you tackle updating accountabilities, responsibility, and all the other elements within a health and safety program.
Did you miss any of my 5 Tips for Health and Safety Management?
Here is a quick recap of 5 tips for a simplified approach to health and safety management for small business owners:
Policies Are Boss
Forecast Health & Safety Costs
Formal Hazard Assessments
Scheduled Your Responsibilities
Continuous Improvement
#transmitsafety // health & safety on all frequencies
Socialize